Author: Jack Jager
While there are three main reasons organizations typically perform Root Cause Analysis (RCA) following an issue with their asset or equipment, there are a whole host of other indicators that RCA should be performed. 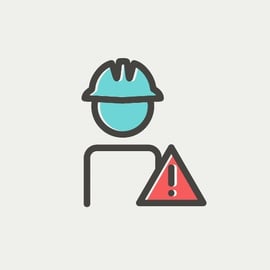
Odds are, you’re recording a lot of valuable information about the performance of your equipment - information that could reveal opportunities to perform root cause analysis, find causes, and implement solutions that will solve recurring problems and improve operations. But are you using your recorded information to this extent?
First, let’s quickly talk about three reasons why root cause analysis is typically performed.
1. Because you have to
There may be a regulatory requirement to demonstrate that you are doing something about a problem that’s occurred.
2. You have breached a trigger point
Your own company has identified the triggers for significant incidents that warrant root cause analysis.
3. Because you want to
An opportunity has presented itself to make changes for the better. Or perhaps you’ve decided you simply don’t want to lose so much money all the time.
At the core of all industry is the desire to make money. Anything that negatively impacts this goal is usually attacked by performing root cause analysis.
I was having a conversation with a reliability engineer at an oil and gas site, and I asked him what lost opportunity or downtime might cost that company over the course of a year. He said it was in the vicinity of three quarters of a billion dollars. $750,000,000. Is this a good enough reason to perform root cause analysis? Even a 10% change would have a huge impact on bottom line figures.
The monetary impact to the business was of course not due to any single event, but to a multitude of events both large and small.
Each event presents itself as an opportunity to learn and to make any changes necessary to prevent its reoccurrence. Once can be written off as happenstance… things happen, serious or minor, and that’s life. But to let it happen continuously means that something is seriously wrong.
While these are all valid reasons to perform root cause analysis, there are at least ten more tell-tale equipment-related clues that an RCA needs to happen – most of which can be identified through the information you’re probably already recording.
Here are ten tell-tale signs that your organization needs to perform Root Cause Analysis:
- Increased downtime to plant, equipment or process.
- Increase in recurring failures.
- Increase in overtime due to unplanned failures.
- Increase in the number of trigger events.
- Less availability of equipment.
- High level of reactive maintenance.
- Lack of time… simply can’t do everything that needs doing.
- Increase in the number of serious events… nearing the top of the pyramid.
- Longer planned “shut” durations.
- More frequent “shut” requirement.
These indicators imply that we need to be doing more in the realm of root cause analysis before these issues snowball.
If you can identify with some of these pain points, download our eBook “11 Problems With Your RCA Process and How to Fix Them” in which we provide best practice advice on using RCA to help eliminate some of these problems.